These articles are now archived and will no longer be updated.
Smarter, greener steelmaking: three new studies to be funded by Swansea-based research programme
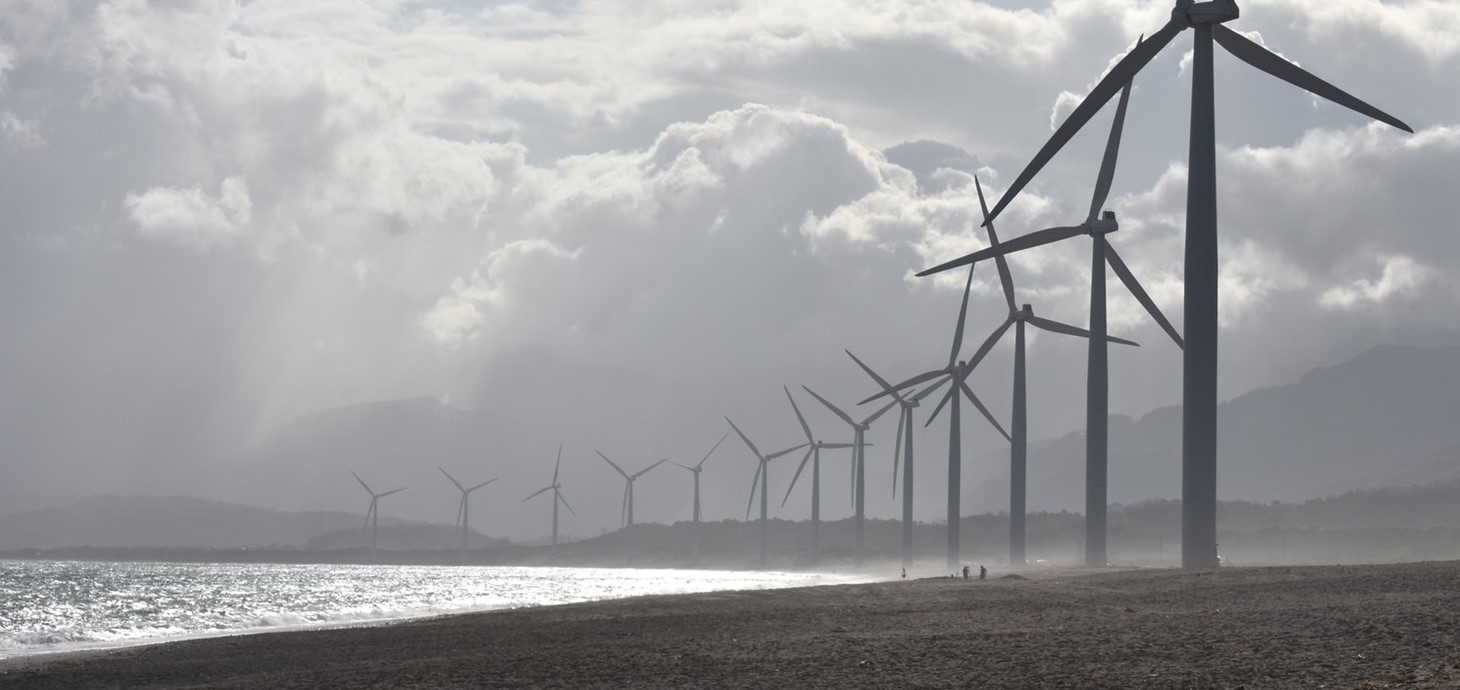
Steel is central to clean renewable energy – the tower and many other components of a wind turbine are made of steel
Three research projects that could help the steel industry become smarter and greener have been given the go-ahead as part of a national steel research programme led by Swansea University.
The projects will explore new electronic monitoring systems that work in ultra-high temperatures, and two potential methods for reducing further the carbon emissions produced during steelmaking.
The work will be funded by the SUSTAIN programme, a £35 million research network led by Swansea University with the universities of Sheffield and Warwick. Its aim is to transform the UK steel sector into a carbon neutral, zero waste, digitally agile industry that is responsive to the fast-changing needs of customers.
SUSTAIN involves more than twenty partners across the UK steel industry: primary manufacturers, supply chain, trade bodies, academic experts and research organisations.
Earlier this year the SUSTAIN team launched their first call for feasibility study projects, open to steel experts across the UK. The three projects - outlined below - are the first to be selected for funding.
Dr Cameron Pleydell-Pearce, steel expert at Swansea University and SUSTAIN’s deputy director, said:
“Research and innovation are the bedrock of a modern steel industry. SUSTAIN brings together almost the whole UK steel sector, with researchers and companies collaborating on an unprecedented scale.
We are already on the road to clean, green and smart steelmaking, but these three studies have the potential to take us further and faster. We are pleased to be able to support them as part of the SUSTAIN programme and we look forward to seeing how they develop over the coming months.”
Ultra-High Temperature Reliable Electronics Development (UHTRED): Dr Alton Horsfall and Dr Andrew Gallant, University of Durham
In the steel industry, operating temperatures above 400 °C are commonplace and monitoring materials and systems in these conditions is essential. However, semiconductor-based transistors are unsuitable for use in extreme temperature environments.
This study will explore the use of materials, designs and circuit models based around microscale vacuum channel transistors. The target is to produce device and circuit designs which are capable of operating over a wide temperature range, from 25 to 1000 °C.
Techno-economic Feasibility of Net-Zero Emission Solutions for Metal Heating (THERMOS): Dr Yukun Hu, University College London
This study will focus on the metal heating process and the proposed sustainable net-zero emission solutions, which involve hydrogen gas. The project will investigate if the UK could introduce carbon-free heating for furnaces at all its rolling mills.
A furnace ‘digital twin’ will be used to demonstrate the proposed net-zero emission solutions. This will analyse combustion behaviours and scale formation, using computational fluid dynamics and reaction kinetics models. The work will provide new insights into the transition pathway of reheating furnaces that might be systemic weaknesses in a green steel economy.
Drop-tube Furnace to Investigate Novel Reductants for the Decarbonisation of Ironmaking: Dr Julian Steer, Cardiff University
This project will test the feasibility of using a non-recyclable carbonaceous waste (Subcoal®) as an alternative reductant material for potential injection in a blast furnace. It involves Cardiff and Swansea Universities, TATA Steel UK and N+P Recycling
Subcoal®, is a non-recyclable paper and plastics product which is high in carbon. The aim is to compare Subcoal as a non-fossil fuel alternative to coal-based reductants. If successful, this will reduce the reliance on mined coal; reduce the landfilling of non-recyclable paper and plastic; and significantly improve the UK steel industry’s carbon emissions footprint as 50% of the Subcoal® carbon is derived from biomass.